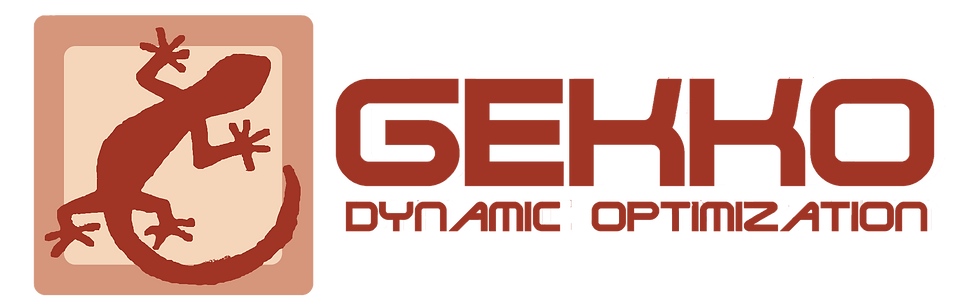
APMonitor Modeling Language Crack Download The APMonitor Modeling Language is based on the standard semantics of the Modelica language, but adapted to operate in real-time systems. This modeling language is not tied to any specific simulator. APMonitor modelers can use any simulator that supports the Modelica language. The applications of the Modelica language range from control system design to factory assembly. APMonitor is an optimization language that supports modeling of dynamic systems in which control variables are linked via constraint equations. APMonitor is a multi-field optimization language that is particularly suited to analyze and control complex, high-volume manufacturing systems. APMonitor includes an Object-Oriented Component Library that contains the functionality that can be used in Modelica-based applications. This library is used extensively in APMonitor process design and optimization. APMonitor currently supports the modeling and optimization of real-time systems. APMonitor represents complex production systems by linking several interacting control variables using constraint equations. APMonitor uses an explicit dynamic simulator. This provides extremely high fidelity, accurate dynamic models for simulation. APMonitor provides powerful signal and data processing capabilities. These are incorporated into an interactive user interface where the user can explore and exploit the behavior of the process. APMonitor is a modular tool for process control and optimization. Customizable from a single, interactive user interface. No need to re-implement the problem domain. Minimizes engineering time and cost. Can support complex and changing processes. Provides automatic control for interactive real-time process control. APMonitor has features for process control and optimization Model-Based Design and Real-Time Optimization Dynamic Simulation and Nonlinear Predictive Control Toolkit for Analysis, Design, and Optimization Verification and Validation Capabilities Coupled to a wide variety of simulators including: Sonic Visualizer Process Flow Modelica Simulator Automation Studio PowerSystems Designer Model_Simulator RobotShop Modelica Simple Parametric Modeler Model_Inspector Modelica ModelMaker Objective Solutions Process Decision Analyze Engine Computer Aided Process Engineering (CAPE) Petroleum See also Modelica Process optimization Chemical engineering References Category:Mathematical optimization softwareQ: APMonitor Modeling Language Crack+ (2022) 1a423ce670 APMonitor Modeling Language Crack Activation Code With Keygen (April-2022) The Keymacro Process Control and Optimization Software Package is an integrated system that provides the basis for system and factorywide optimization, monitoring, and management. It combines network communication, physical process sensing, and advanced control into a single package for remote process control. Keymacro is the industry's most powerful remote network optimization software. Keymacro has been an integral part of the process control technology market for over a decade and is one of the most successful process control products ever developed. A single package of hardware, software, and process control systems enables process optimization, new product development, and improved process control. Pulse Width Modulation - Modulation of the output power by superposing an oscillating signal with a fixed frequency pulse width. Pulse Width Modulation (PWM) is a technology used in low voltage, high power power supplies to control or regulate the amplitude of the waveform. The pulse width modulation is a digital control method for delivering an output signal whose voltage is a function of the input signal. The resulting output waveform can be connected to the input to provide amplification, multiplication, or other processing. In power-transistor circuits (e.g. power drivers, power supplies, motor control) PWM is widely used for power regulation and converting direct current to alternating current. PRIMER - An advanced PWM controller. The PRIMER is an application-specific integrated circuit (ASIC) that combines all of the functions needed to control a high-current AC motor in a single, self-contained package. It allows the analog voltage applied to the controller to change. It is capable of bi-directional modulation and includes a digital-to-analog converter, high speed PWM, and an optional oscillator that can be used for synchronizing the PWM clock and the output voltage. It offers optional protection features like overcurrent protection, thermal overload protection, and overload shutdown. And it offers high efficiency. The PRIMER can be connected to a 4-20mA current loop or a signal or feedback loop. PROCESS CONTROL - is a science that is designed to monitor and control production processes. Process control involves the monitoring and measuring of key variables of the process to assure the process meets the desired target. Process control also involves the adjustment of one or more variables in the process. This is done through a feedback loop. The key to process control is monitoring the process and responding with the appropriate What's New in the APMonitor Modeling Language? System Requirements: Windows 7, Windows 8, Windows 10 Mac OS X 10.10 or later (Mac OS X 10.11.4 and later required for multiplayer) Recommended: Intel i3 3.3 GHz or better Intel i5 3.4 GHz or better Intel i7 3.6 GHz or better 2 GB RAM or better DirectX 12 or later High-end GPUs recommended for graphic settings Minimum: OS: Windows 7 SP1 (32-bit or 64-bit) Process
Related links:
Comments